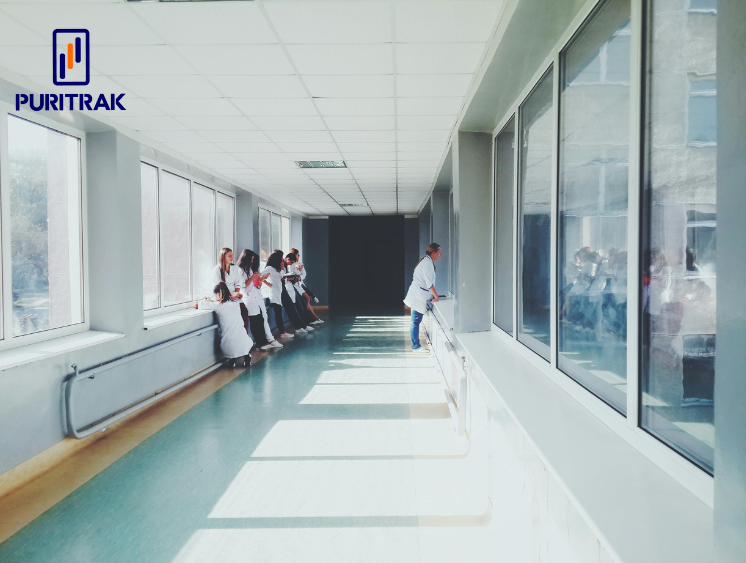
In the hospital environment, infection control plays an important role in protecting the health of patients and medical staff. Hospital cleanrooms are a key solution for minimizing the risk of infection. So what are hospital cleanrooms used for? Assessed on what standards? Let’s find out in the article below!
1. What are hospital cleanrooms?
Hospital cleanrooms are designed to minimize dust particles’ penetration into the air while controlling certain other parameters, such as humidity, pressure, and temperature, when necessary. This control helps reduce the risk of infection or cross-contamination and ensures sterile conditions.
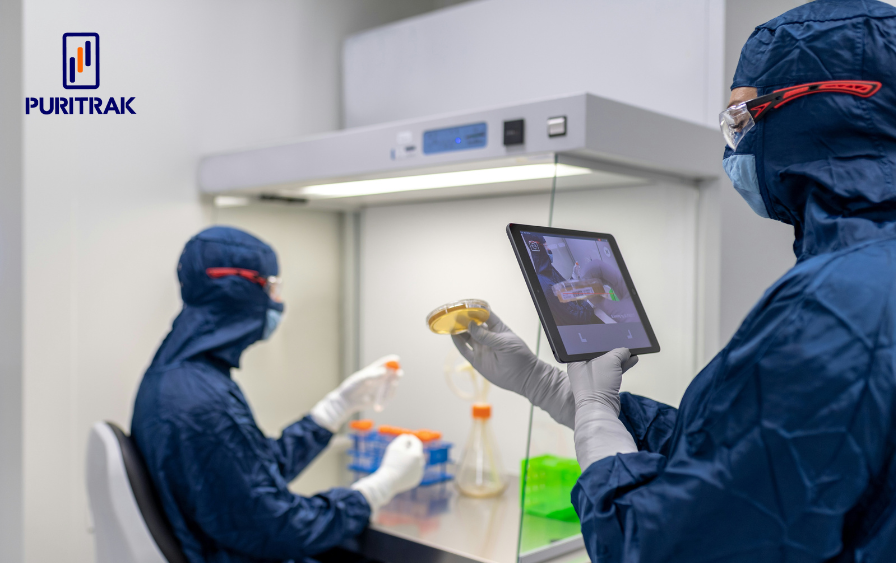
Hospital cleanrooms are designed to control contamination and maintain a sterile environment. This is achieved by practicing strict hygiene protocols, including separating clean areas from other hospital activities. Key measures include providing HEPA-filtered air and precisely controlling pressure, humidity, and temperature to prevent cross-contamination.
2. What are hospital cleanrooms used for?
Cleanrooms in hospitals play a crucial role in infection control, ensuring safety for patients, medical staff, and the surrounding environment. The main functions of hospital clean rooms include:
– Preventing cross-infection between patients, medical staff, and the environment is crucial. Cross-infection is a leading cause of hospital-acquired infections. Cleanroom systems effectively reduce the spread of bacteria, viruses, and pathogens through meticulous air quality control.
– Vulnerable patients, including those with weakened immune systems like cancer patients undergoing chemotherapy, post-organ transplant recipients, and premature births, are susceptible to infections from their surroundings. Therefore, hospitals employ cleanrooms with specialized air filtration systems. These systems prevent contaminated air from entering, ensuring a safe and clean environment for these patients.
– The isolation of patients with contagious diseases is paramount in hospital settings, aiming to prevent the dissemination of pathogens. Cleanrooms are crucial for patients with conditions such as tuberculosis, SARS, COVID-19, or severe influenza. They serve as a critical barrier, preventing the escape and dissemination of infectious agents. Negative pressure rooms and air filtration systems within these rooms ensure that bacteria and viruses are contained, effectively controlling outbreaks.
– Maintaining a sterile environment during surgery and specialized treatments. Operating rooms demand the most stringent hygiene standards within a hospital setting. Surgical infections can result in severe complications for patients. Clean rooms play a vital role in controlling air quality, effectively removing bacteria, dust, and particulate matter that pose infection risks.
3. The standards of hospital cleanrooms
Hospital cleanrooms are designed to ensure a clean, dust-free, and contamination-free environment. When designing these rooms, it is essential to comply with standards such as ISO 14644-1, and FED STD 209E. Cleanrooms in the medical industry must also adhere to GMP standards, including EU GMP and WHO GMP. FED STD 209E is an older standard that is sometimes referenced.
In addition, hospital cleanrooms in Vietnam must adhere to the following national standards:
– Climate data for construction design: Standard 4088-1985
– Ventilation, air conditioning, and heating system design: Standard TCVN 5687-1992
– Fire prevention and firefighting standards for buildings: Standard TCVN 2622-1995
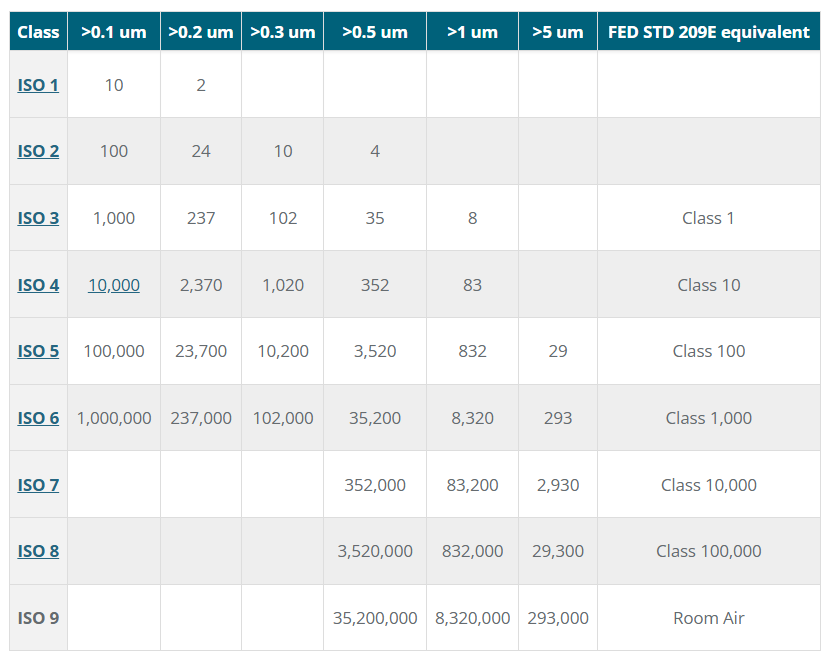
According to the ISO 14644-1 cleanroom standard, a cleanroom is an environment where airborne particle concentration is controlled to a low level. Cleanrooms are classified from ISO 1 to ISO 9, based on the maximum allowable concentration of particles per cubic meter or cubic foot. ISO 8 is among the lower cleanroom classifications and is considered one of the less stringent classes within the standard.
For instance, the airborne particle concentration in a typical office is 5-10 times higher than in an ISO 8 patient room. Furthermore, microbial count assessments in specialized hospital rooms across Vietnam reveal significantly compromised air quality. These assessments demonstrate that air quality frequently reaches, and in some instances falls below, the minimum acceptable standards.
Related Articles: The latest 2025 standard for cleanrooms
4. Classification of cleanrooms
Not every area in a hospital needs a controlled environment. However, certain areas require strict controls, and the following cleanliness levels apply to each room/area:
Operating rooms: demand a high level of cleanliness. In Vietnam, they must adhere to ISO 7 standards, equivalent to Class 10,000, which stipulates a maximum of 325,000 particles of 0.5 microns or larger per cubic meter of air. For advanced operating rooms, ISO 5 standards, equivalent to Class 100, are required, limiting suspended particle counts to 3,520 particles or fewer per cubic meter.
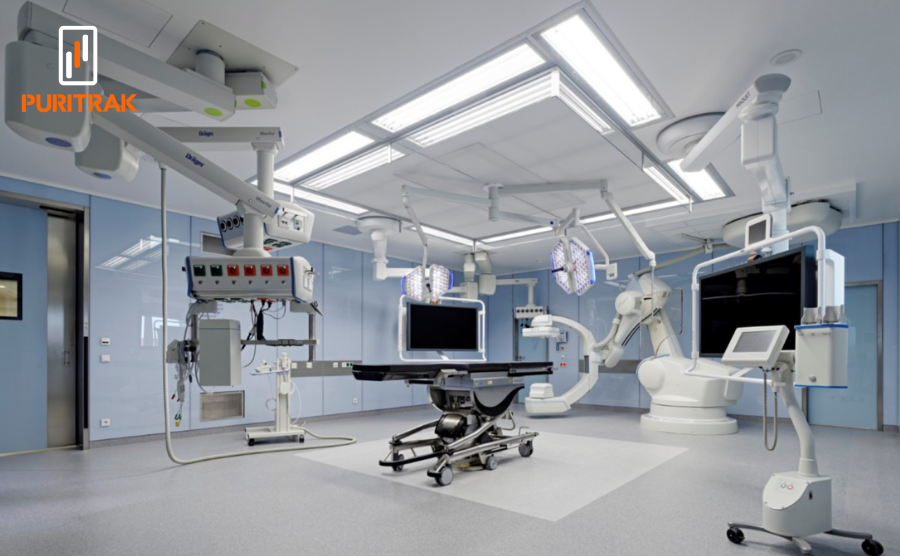
Operating rooms are critical to patient safety, as minimizing surgical site infections and severe medical complications is paramount. Therefore, adherence to specific construction standards is essential for all hospitals.
Maintaining sterility in operating rooms requires a clean air handling system, such as Blower Filter Units (BFUs), to prevent the ingress of dust and bacteria. Air is pre-treated with UV-C irradiation prior to HEPA filtration to enhance its efficiency. Air exchange rates, which vary from 15 to 20-25 air changes per hour, are determined by the specific room type.
This approach mitigates the risk of infection during and following surgical procedures. Maintaining a sterile environment within the operating room is crucial to minimize postoperative infections, which directly impact treatment outcomes and patient recovery time.
Minor surgery room: The minor surgery room meets ISO 8 equivalent to Class 100,000.
Operating corridor: The operating corridor is usually designed at ISO 8 or Class 100,000 cleanliness level.
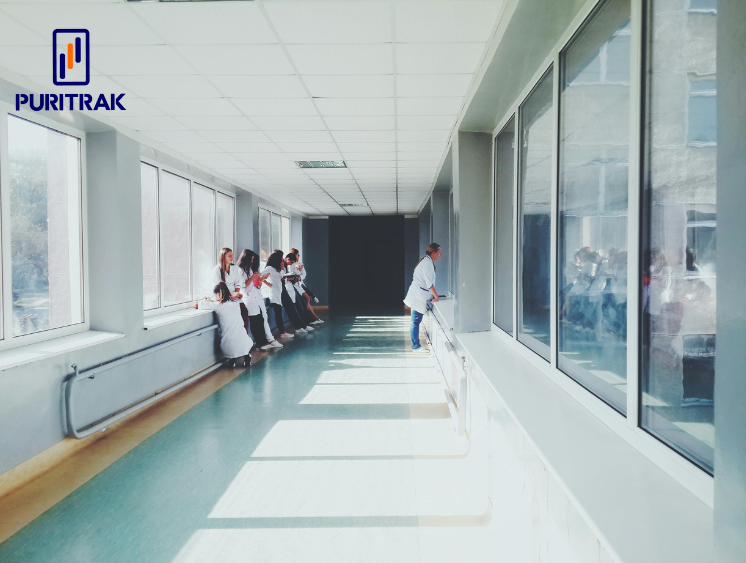
ICUs: Intensive Care Units (ICUs) in hospitals require a strictly controlled air cleanliness environment to protect patients from infection, particularly in isolation ICUs. These rooms typically adhere to ISO 7 or 8 standards, depending on the specific ICU type.
Hospital rooms: Hospital rooms have less stringent cleanliness requirements compared to operating rooms and ICUs. However, air quality control remains essential to prevent cross-infection. Cleanliness standards for patient rooms typically range from ISO 8 to ISO 7.
To maintain optimal air quality and minimize infection risks, patient rooms in hospitals are equipped with HEPA filtration systems. General patient rooms require an air exchange rate of 4 to 6 air changes per hour, while isolation rooms, requiring a higher level of protection, necessitate 6 to 12 air changes per hour.
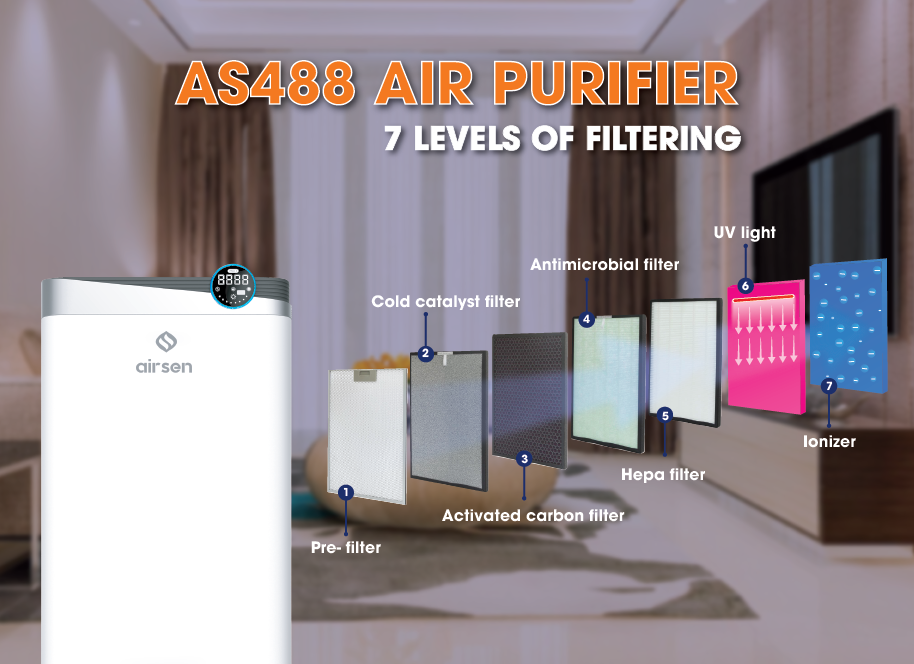
Maintaining optimal air quality is vital within hospital environments. Airborne dust particles, bacteria, and viruses pose significant health risks to both patients and medical personnel.
Sterile area: Controlled area
Resuscitation rooms: Controlled area
Related Articles: Air Purifier Airsen AS488, AS800
5. Hospital cleanroom construction unit
Puritrak is a hospital cleanroom construction unit that meets stringent hospital standards. After carefully researching the clean room location and accompanying equipment, Puritrak begins construction in 5 key steps:
Step 1: Client Requirement Assessment: Puritrak meticulously assesses client requirements and conducts thorough site surveys to determine precise installation parameters.
Step 2: Design Review and Approval: Detailed design reviews are conducted, and necessary refinements are made, culminating in formal client approval prior to implementation.
Step 3: Construction Execution: Utilizing specialized materials and adhering to strict quality control measures, Puritrak executes construction in full compliance with relevant hospital standards.
Step 4: Pre-Operational Inspection and Acceptance: Rigorous inspections are performed to ensure compliance with design specifications and operational requirements, followed by formal client acceptance.
Step 5: Warranty and Maintenance Services: Puritrak provides comprehensive warranty and maintenance services for cleanroom construction and associated equipment, including cleanroom equipment such as Pass Boxes, AHUs, Air Shower, and FFUs, and laboratory equipment such as Biological Safety Cabinets, Laminar Flow Hoods, and Dispensing Booths.
Related Articles: Clean Room Construction for Hospitals
A hospital cleanroom is an environment that is rigorously controlled in terms of dust particles, microorganisms, humidity, pressure, and temperature. The purpose of the cleanroom is to minimize the risk of infection, and cross-infection, create a sterile environment, and ensure the safety of patients and medical staff.
Understanding the importance of hospital cleanrooms is vital for ensuring patient and staff safety.
If you require advice on air filtration systems, please contact the information below. Puritrak’s highly trained technical team is ready to support and answer any questions. Thank you for your interest!
Puritrak products and services:
Puritrak indoor air quality measuring device
Puritrak outdoor air quality measuring device
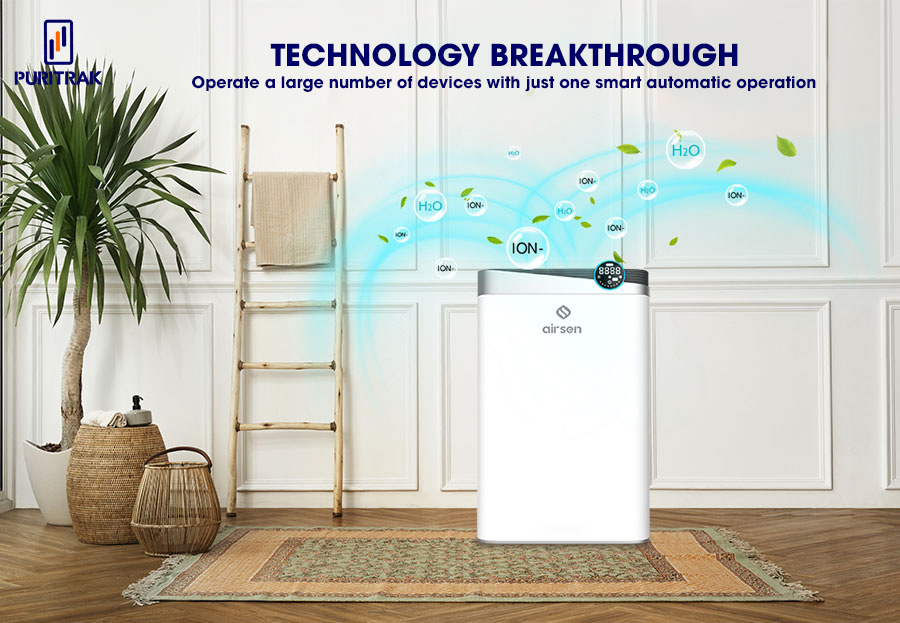
Contact info:
- Hotline: 0904.800.006
- Website: puritrak.com
- Email: [email protected]
- Fanpage: Puritrak