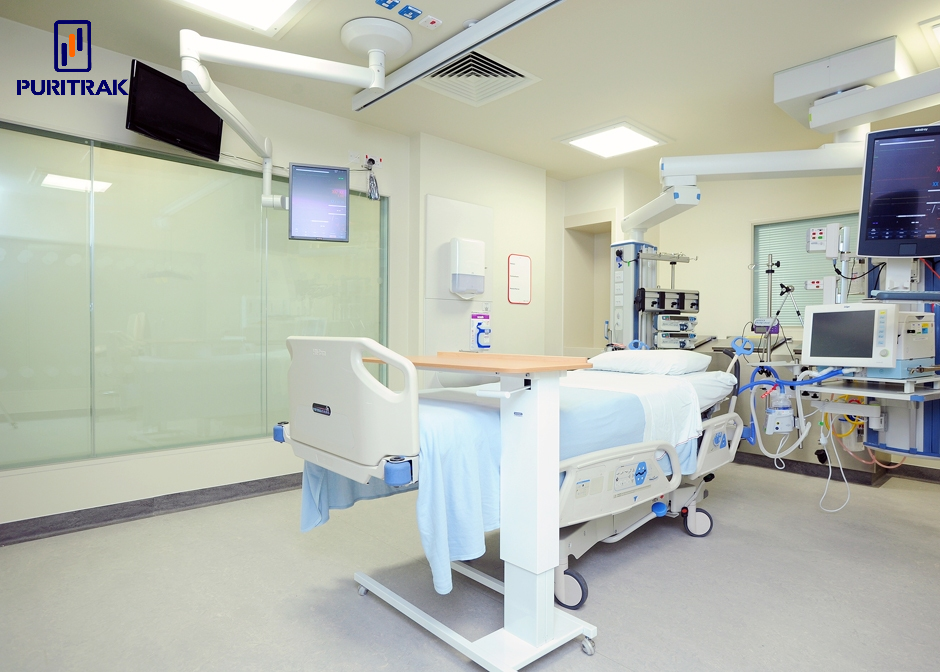
Clean rooms in hospitals play a crucial role in controlling infection and ensuring an aseptic environment for healthcare activities. In 2025, cleanroom standards will be more strictly updated to improve the air quality. So, let’s follow this write to update detailed information.
1. Introduction of clean rooms
1.1. The concept of clean rooms
Clean rooms are specialized areas in the hospitals, which can strictly control various factors such as dust particle, density and size, temperature, humidity, pressure, and cross-contamination risk. Clean rooms are often adopted in the operating rooms, minor surgery rooms, and sterilization areas with air purification systems and infection control measures that extend from the room’s entrance to medical instruments, ensuring to meet strict medical hygiene standards.
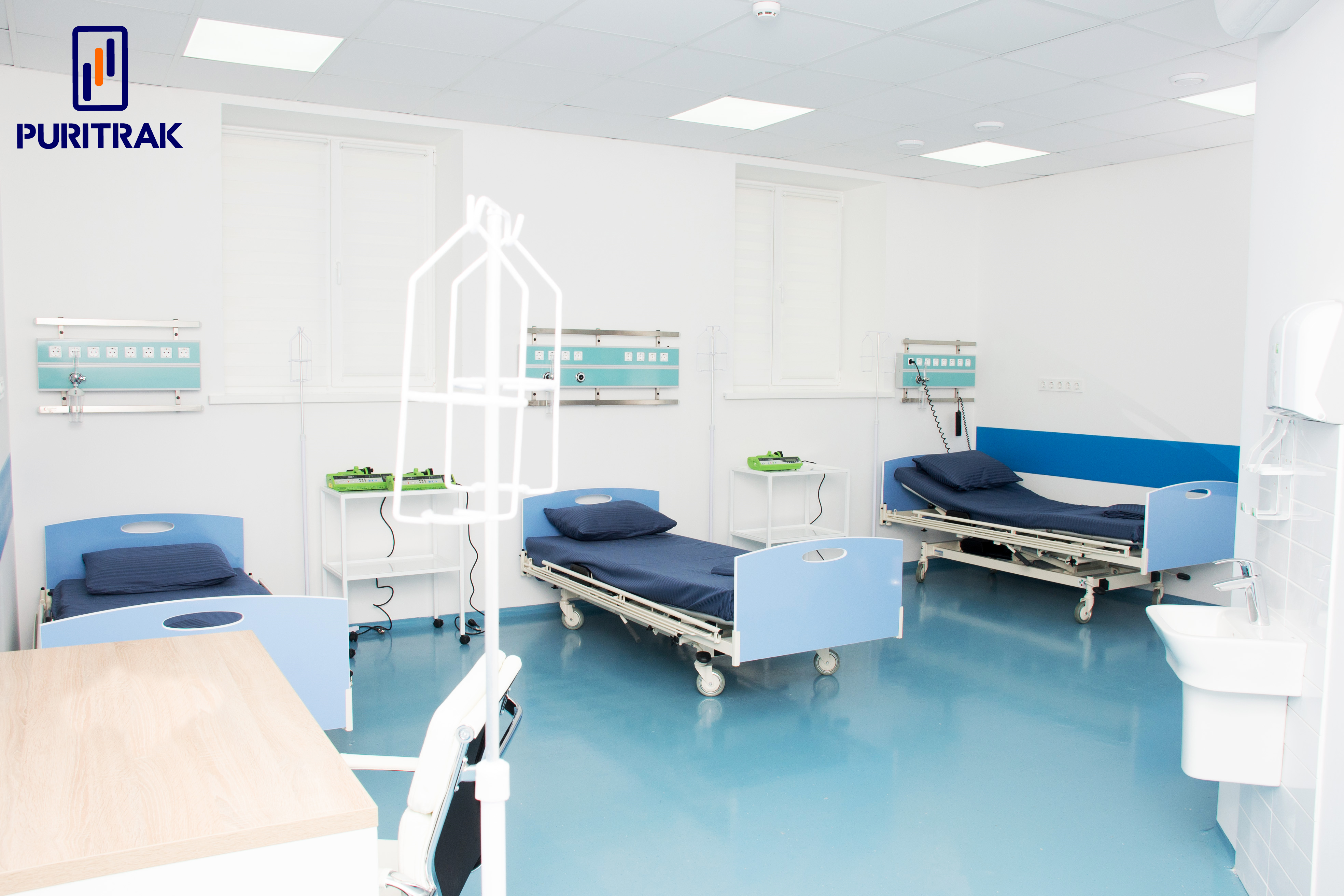
1.2. The importance of clean rooms in the medical environment
Clean rooms in the hospitals ensure an aseptic environment, preventing infections for the patients’ surgical areas, helping to increase the success rate of surgery, and protecting the health of patients and doctors. The Ministry of Health emphasizes clean room systems in the operating rooms and treatment areas.
Furthermore, clean rooms are also important in the pharmaceutical and medical food production, preventing pollution, and ensuring the quality of products. This is the key factor to enhance the effectiveness of treatments and constructing safe healthcare systems.
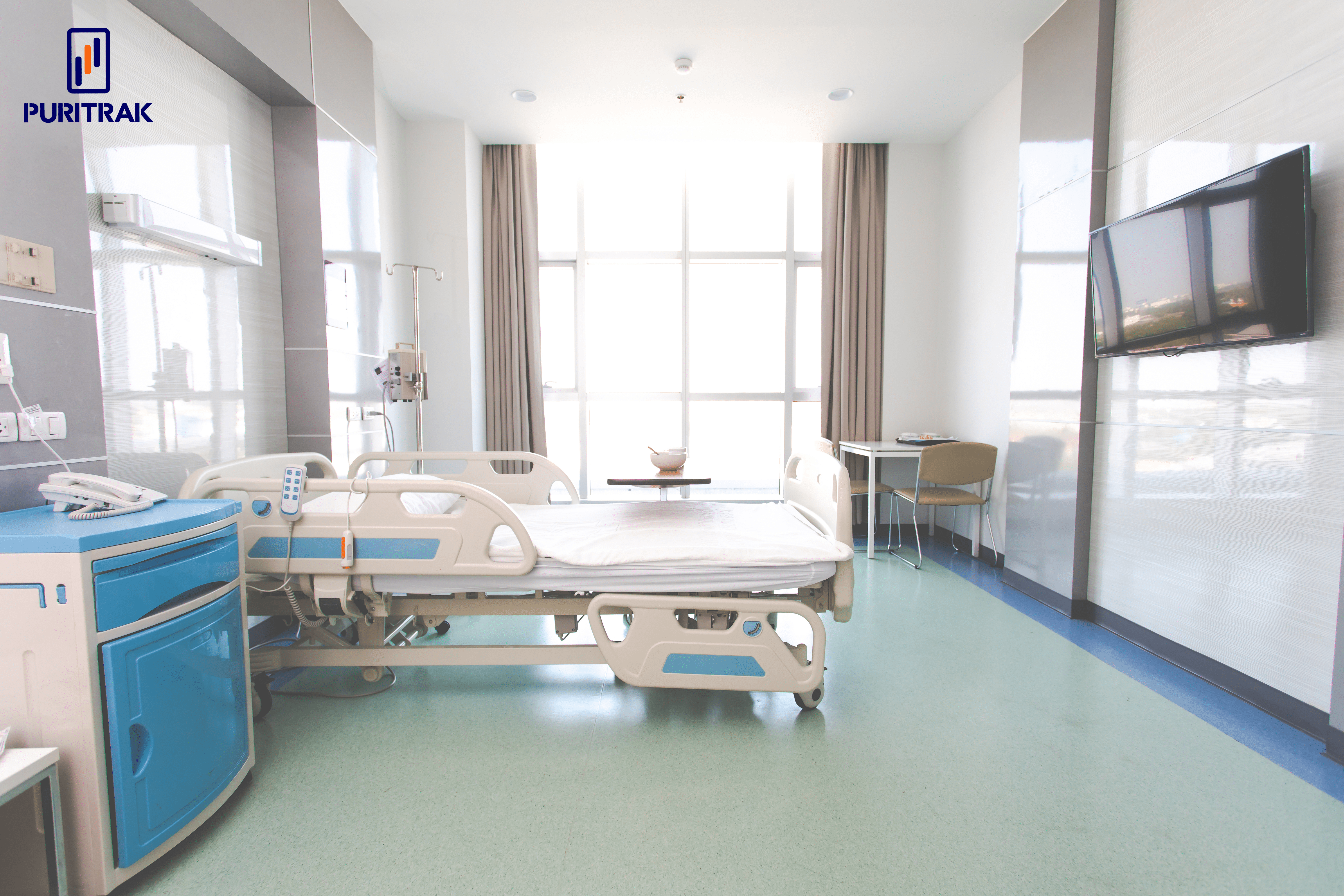
1.3. The benefits of clean rooms for patients and healthcare workers’ health
For patients, the aseptic environment helps to decrease the risk of infections, especially in surgery and treatment of severe diseases.
For healthcare workers, clean rooms facilitate safe working, limiting contact with bacteria and toxic chemicals due to modern air filters. This contributes to leveraging the quality of healthcare and ensuring an effective working environment.
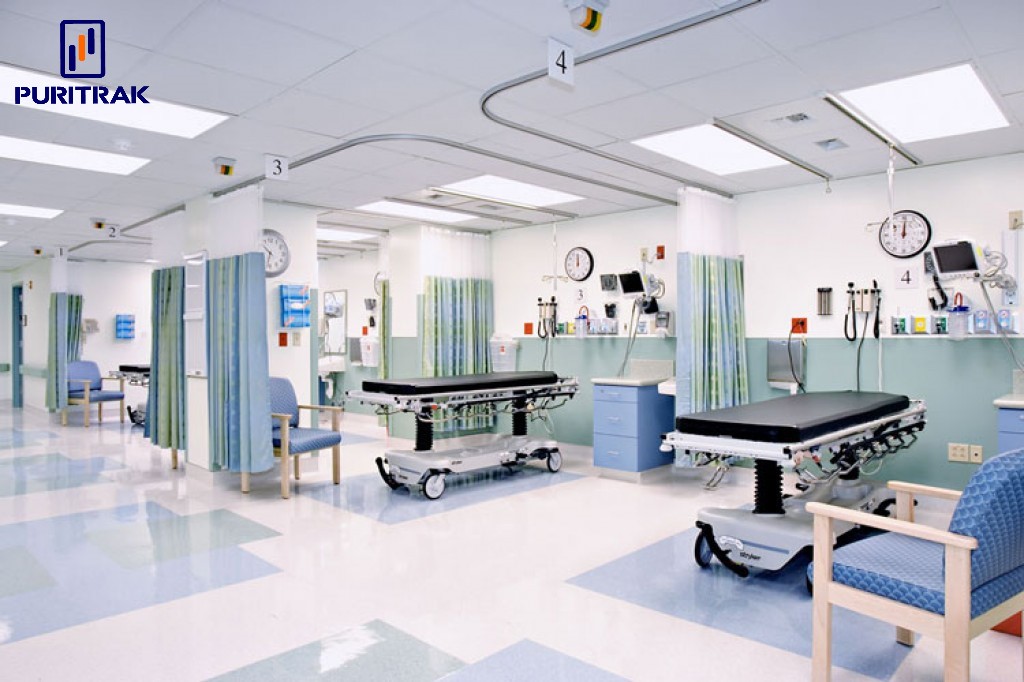
2. The 2025 latest standards for clean rooms
2.1. International standard
- ISO 14644-1: The international standard for clean rooms, regulating cleanliness level from ISO Class 1 to ISO Class 9 based on the quantity of dust particles in the air. This is widely applied in many sectors such as pharmaceutical products, microelectronics, healthcare, and high technology production.
- GMP WHO: The World Health Organization ( WHO )’s guideline for implementing good production requires controlling the quality, manufacturing environment conditions, and the process of ensuring the safety and effectiveness of pharmaceutical products.
- GMP EU: The GMP standard of the EU has stricter regulations than that of the GMP WHO, especially in aseptic production. Clean rooms are categorized according to Grades A, B, C, and D, which are equivalent to levels of controlling dust and microbes.
- FDA: GMP Standard of Food and Drug Administration ( FDA ) requires enterprises to continuously update technologies and processes to ensure safe and qualified products. This is applied in many sectors such as pharmaceutical products, food, and medical equipment.
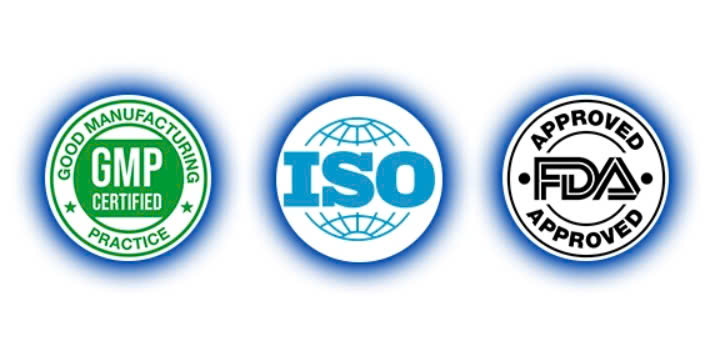
2.2. Vietnam’s standard
- Climate data for construction design: Standard 4088-1985
- Design of automatic sliding doors for ventilation, air regulation, and heating: Standard TCVN 5687-1992
- Fire prevention and protection standards for buildings and structures: Standard TCVN 2622 – 1995
2.3. Cleanliness levels for different areas in hospitals
- Operating room: The area requires an extremely high level of cleanliness. The proposed cleanliness level for operating rooms is ISO 5 – ISO 7, equivalent to Class 100 – Class 10.000. Today, most operating rooms in hospitals are at Class 10.000.
- Minor Surgery Room: Currently, minor surgery rooms are typically at Class 100.000, equivalent to ISO 8.
- Surgical Corridor: Typically designed at Class 100.000 cleanliness level.
- Sterile Area: Controlled environment.
- Recovery Room: Controlled environment.
- ICU, CCU: Controlled environment.
3. Technical requirements for clean rooms in hospitals.
3.1. Air Filtration System
- HEPA Filter (High-Efficiency Particulate Air): Removes at least 99.97% of dust particles ≥0.3 micrometers in size.
- ULPA Filter (Ultra-Low Penetration Air): Removes up to 99.999% of dust particles ≥0.12 micrometers in size.
3.2. Room Pressure
- Positive Pressure Room: Prevents contaminated air from entering and is applied to operating rooms and sterile areas.
- Negative Pressure Room: Prevents infectious air from spreading outside; used in isolation rooms for contagious diseases.
3.3. Temperature, Humidity, and Ventilation
- Temperature: Maintained between 21°C and 26°C.
- Relative Humidity: Between 60% and 70%.
- Ventilation: Air exchange rate of 15 to 20 times per hour.
3.4. Antimicrobial Building Materials and Surfaces:
- Use smooth, waterproof, easy-to-clean, and antibacterial materials for walls, floors, and ceilings.
- Rounded corners to prevent dust and bacteria accumulation.
3.5. Pollution Control System:
- Use monitoring and control equipment to track air dust, bacteria, and chemical levels.
- Ensure compliance with air cleanliness standards, such as ISO 14644-1 and TCVN 8664-1:2011.
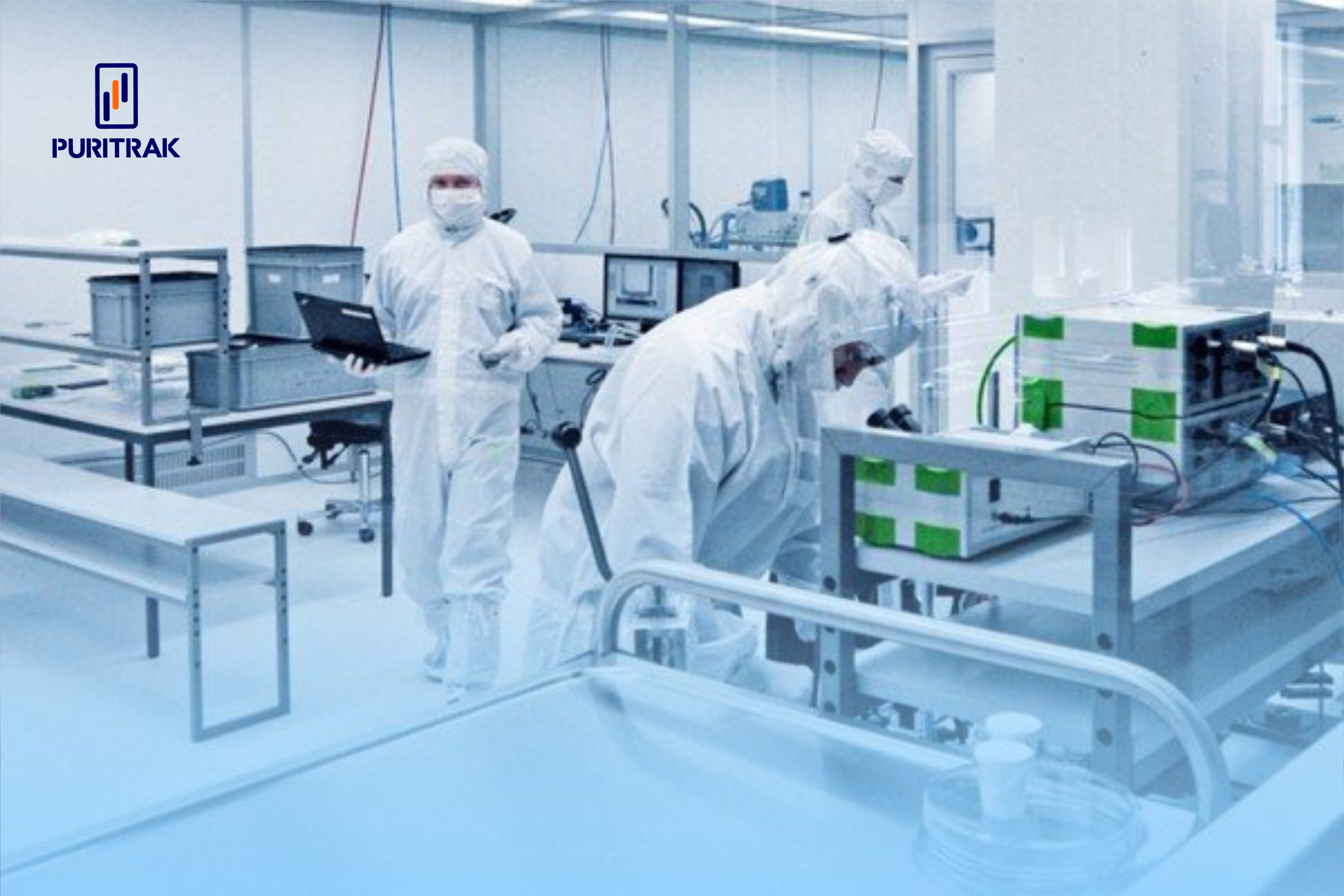
4. Applications of Clean Rooms in Hospitals
4.1. Operating Rooms and Emergency Recovery Units
Ensure a sterile environment, reducing the risk of infections during surgeries and critical patient care.
4.2. Intensive Care Units (ICU, NICU)
Provide clean air for patients with weakened immune systems, minimizing the risk of infections.
4.3. Laboratories and Pharmaceutical Production
Control bacteria and dust levels to ensure accurate testing and maintain the quality of medicines and medical devices.
4.4. Infectious Disease Isolation Rooms
Prevent the spread of bacteria and viruses using negative pressure systems and specialized air filtration.
4.5. General Patient Rooms
Improve air quality, helping patients recover better and reducing the risk of cross-infection.
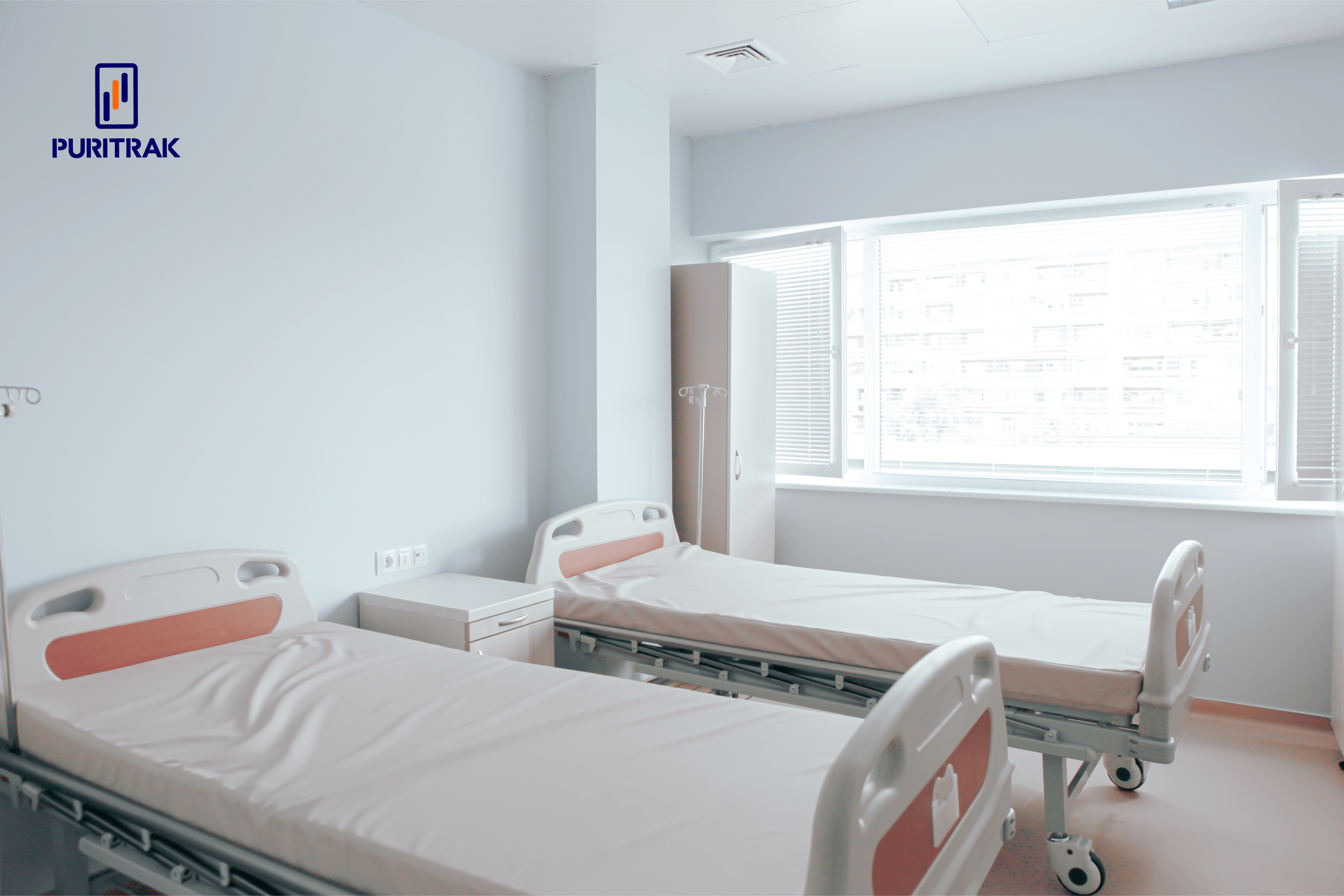
5. Solutions for Achieving Hospital Clean Room Standards
5.1 Selecting an appropriate air filtration system
The air filtration system plays a crucial role in removing fine dust, bacteria, and viruses from the air. Equipment such as HEPA air purifiers and HVAC systems with high-efficiency filters help ensure that clean air meets hospital standards.
Read more: Puritrak Airsen AS800 air purifier
5.2. Cleaning procedures and regular inspections
Regularly clean and maintain the air filtration system. Replace filters on time and monitor air quality to maintain a fresh environment and minimize infection risks.
5.3. Solutions to Improve Air Quality in Hospitals
In addition to filtration systems, integrate air quality sensors, humidity control, and UV-C disinfection to enhance efficiency.
5.4. Technologies and Equipment for Compliance
Utilize advanced technologies such as electrostatic filtration, ionization, controlled ozone, and positive/negative pressure ventilation to optimize air quality in critical areas like operating rooms and intensive care units.
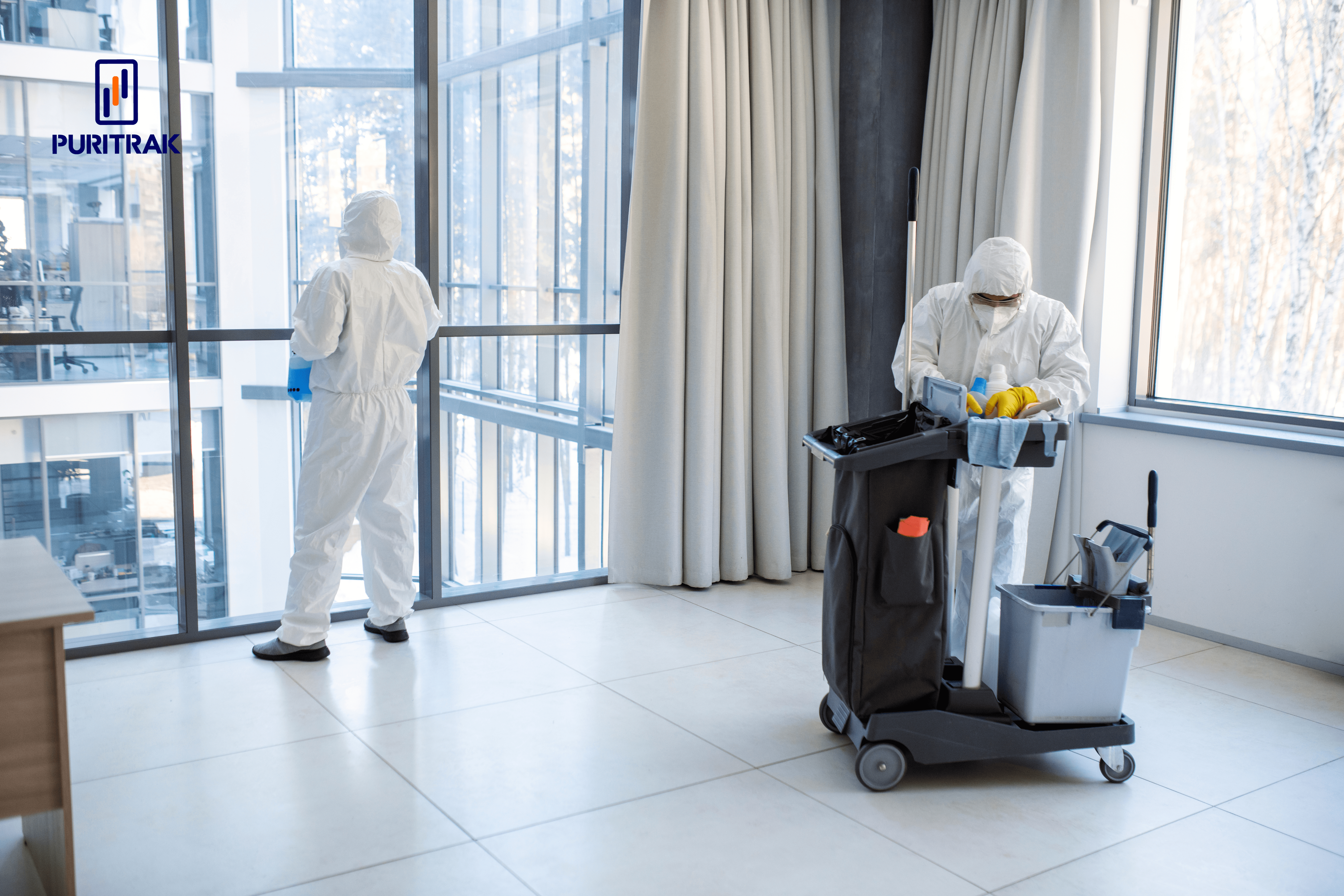
Hospital cleanrooms serve a vital function in preventing infections, protecting patients and medical staff, and improving treatment quality. Implementing cleanroom standards, including air filtration, sanitation, and environmental control, helps minimize the risk of cross-contamination. Investing in modern equipment, such as the Airsen AS800 air purifier with an advanced HEPA filter, creates a clean and safe environment, reduces allergy symptoms, and enhances patient health protection.
Puritrak products and services:
Puritrak indoor air quality measuring device
Puritrak outdoor air quality measuring device
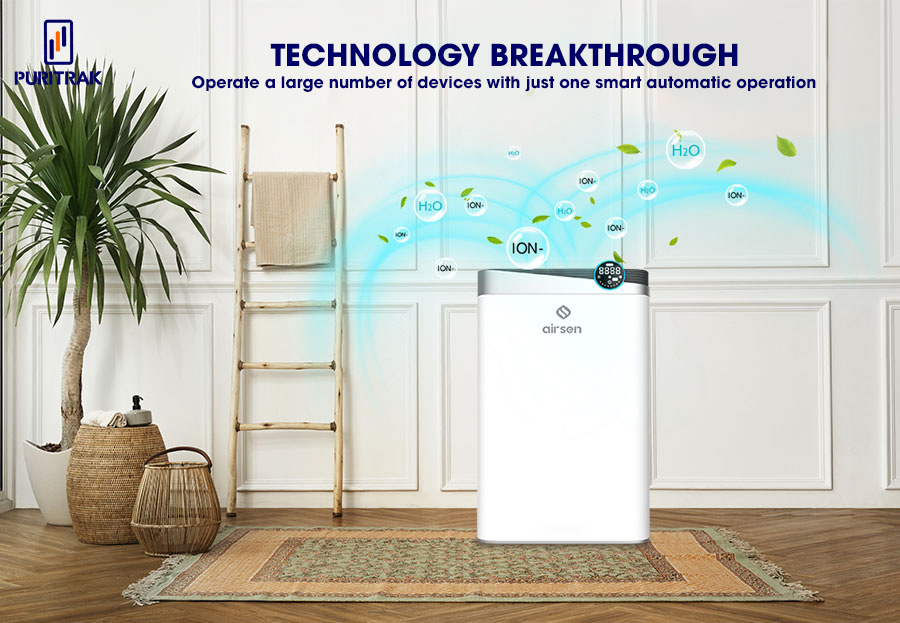
Contact info:
- Hotline: 0904.800.006
- Website: puritrak.com
- Email: [email protected]
- Fanpage: Puritrak